全因子实验设计及其在航空制造中的应用
作者: 徐伟
国内复合材料行业起步晚,发展缓慢。尤其在碳纤维复合材料领域,由于原材料需要进口,发展尤其缓慢。到目前为止,在整个复合材料行业中,复合材料零件大部分都采用手工铺叠方式,真空—热压罐成型技术,只有少数零件采用RTM、RFI等快速成型技术,该类工艺方式还不够成熟,基础研究还有待进一步加强。自动铺带、丝束铺放技术目前正在试用阶段,尚未大规模应用。复合材料制造技术由于工艺过程复杂、影响因素众多且成型过程属于高温高压环境,固化完成后的制件变形控制、内部质量问题等问题一直以来都未能得到有效控制,制造工艺控制难度大,对操作人员技能要求高,对过程参数控制极其严格,需要开展大量的实验设计及验证。
在复合材料零件固化过程中,不同材料体系固化参数不一样。因此需要通过大量实验来探索最佳的固化参数组合。同时对固化后零件的机械加工和力学性能测试也要进行大量实验,以确定最佳的加工参数,如刀具转速、进给量、切屑速度、刀具种类等。在此过程中,需要选择合适的实验设计方法,并通过试验实施以及实验结果分析最终决定相关工艺参数、加工参数等。
实验设计是一门学科,但目前实验设计多用于工艺性实验及分析,在复合材料生产中很少得到应用。不同实验设计方法使用范围不同,应用条件也不一样。因此,有必要开展实验设计在复合材料中的应用研究,提高复合材料基础研究和制造过程质量可靠性,为复合材料的扩大应用提供指导。
实验设计使用的材料和仪器主要包括:幅宽300mm的T300碳纤维预浸料,以及直径0.6米的1.5米热压罐。
实验设计方法简介
目前常用的实验设计方法主要有单因子实验设计、全因子实验设计、部分因子实验设计、响应曲面设计和正交实验设计等5种。详见图1。
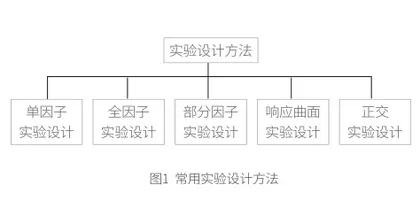
单因子实验设计主要用于研究单个因子对响应变量Y的影响,并对实验结果进行统计学上的验证、分析,找到因子的最佳取值范围。一般可以通过拟合线图,寻找变量Y与因子X的对应关系,通过X来预测 Y的取值范围,如图2所示。

全因子实验设计一般用于研究多个因子、多水平条件下变量对响应变量Y的影响,并对实验结果进行统计学上的验证、分析。找到Y取最大值时的最佳因子取值组合[1]。通常需要对多个因子的不同水平进行定义,其实验次数为:水平因素,例如3因素2水平所需的实验次数为:23=8次。参见表1。全因子实验设计能够考虑所有的可能组合。
部分因子实验设计一般用于研究5~15个(最多15个)2水平因子(高水平和低水平)对响应变量Y的影响,并对实验结果进行统计学上的验证、分析。找到Y取最大值时的最佳因子取值范围。该法相对于全因子实验设计,可以大大减少试验次数,减少试验成本。
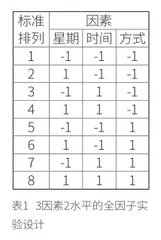
响应曲面实验设计研究3个因子多种水平下且相互之间有影响的因子(高水平和低水平)对响应变量Y的影响,并对实验结果进行统计学上的验证、分析,找到Y取最大值时最佳变量取值范围。分析结果见图3。

正交实验设计研究2个及以上多水平且相互之间无影响的因子(系列水平)对响应变量Y的影响,一般是选择一个因子不同水平,保持其他因子固定进行实验,确定最佳的取值,依次确定其他因子的最佳取值范围,形成最终的最优参数。示例参见表2设计方案。
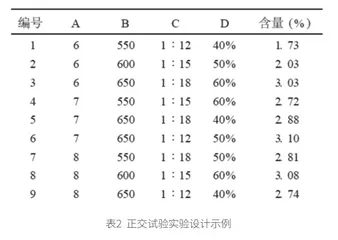
比较上述五种方法,前四种注重实验设计及试验结果的统计分析,具有较强的理论依据,唯一的区别在于因子数量的不同,其技术路线基本一致。正交实验设计是最普通的一种实验方法,无须考虑各因子间的交互影响,在用于化学、材料等学科时,有很大的局限性,而且对实验结果没有统计学上的分析和验证,其可靠性有待进一步验证。
本文针对复合材料固化参数开展了某复合材料制造过程的实验设计及分析。根据以往经验和实验认为固化时间、升温速率和固化压力3个因子是比较重要的因素,且3个因子之间有相互影响。根据上述5种方法的适用范围和特点,本文选择全因子实验设计方法,每个因子分别取高低2个水平进行全因子实验设计。
全因子实验设计开展过程
根据选定的固化时间、升温速率和固化压力3个因子,分别取高低2个水平进行全因子实验设计,并设计了实验设计技术路线图,如图4所示。其中,第一步开展全因子设计并进行试验;第二步对选定的模型进行拟合,验证模型的可靠性;第三步进行残差诊断,如果残差超标,需重新进行模型拟合;第四步对模型进行分析和解释;第五步将结果与目标进行判断,看是否需改进,若无须改进,再次进行试验,对方案进行验证。
将固化时间、升温速率、固化压力作为3个设计因子,分别取一高一低水平,进行3因素2水平全因子实验设计,将固化度作为实验结果,实验设计参数及结果如表3所示。
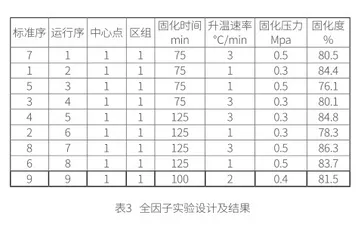
利用分析因子设计,可得到图5模型改进前和模型改进后实验设计结果的统计分析。
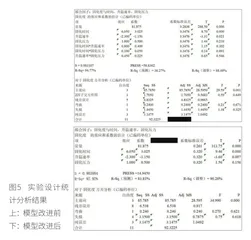
由图5分析结果可以看出,固化时间和升温速率的P<0.05,是2个关键因子,其贡献率达到88.48%。去掉不相关的二阶交互作用,对模型进行改进后的统计分析显示,2个关键因子的贡献率达到了90.26%,残差也变得更小,说明分析结果总体有效。
对改进后的模型开展因子图分析,对固化时间、升温速率和固化压力3个因子间的效应进行主效应分析,并得到固化图的立方图,见图6。
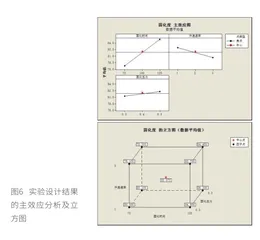
由图6可以看出,固化时间和升温速率是2个主效应,和图5分析结果一致。在固化度立方图中也可以发现,当固化时间为125分钟,升温速率为1℃/min,固化压力为0.5Mpa时,固化度为86.3%,为最高。
为了确定最佳的关键X取值范围,通过对关键因子X进行优化分析,确定当关键X取值范围确定的情况下,得到固化度的最佳值。结果见图7。
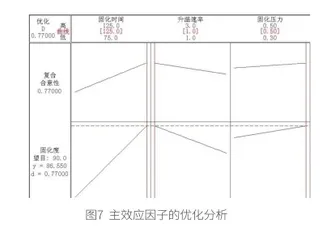
从图7可以看出,当3个因子取值固定后,固化时间为125min、升温速率为1℃/min、固化压力为0.5Mpa时,零件的固化度预期可达到86.55%,与实际的86.3%基本接近。
结论和展望
本次实验设计和结果表明,全因子实验设计对于实验安排、实验结果分析等均有很强的指导意义,特别对有交互作用的多因子分析,其意义更加重大。后续将加强全因子实验设计方法在复合材料过程质量控制研究中的应用实践,积累更多的经验和方法,为提升航空复合材料产品质量和扩大应用提供技术指导。
参考文献
[1] 马晓丽,林航,华学明,吴毅雄.三丝CO2双边角焊全因子试验设计[J] .焊接学报,2013年05期.