组织变革:企业数字化转型的必经之路
作者: 赵娟
随着新一代信息技术与先进制造技术的融合发展,众多制造型企业顺势而为,纷纷在数字化转型的浪潮中扬帆远航。但在制造型企业突破传统发展模式、乘浪前行之余,我们仍然需要警惕其向数字化航进过程中,容易触碰到的暗礁和极易误入的旋涡,提前做好布局和准备。
通过调研和观察,我们看到制造型企业在数字化转型过程中往往会陷入“重短期投入、轻长期规划”“重技术升级、轻精益基础”“重项目实施、轻人才成长”以及“重效益提升、轻理念进阶”四大误区,容易将数字化转型的视角局限在简单的技术升级和项目实施层面,缺乏从员工转型、组织重塑等维度深层次、系统性地思考和实践。
所幸的是,在对西门子数字化工业集团成都工厂深入调研和了解的过程中,我们看到了一套经过实践验证、行之有效的解决方案,即:全方位、渐进式的 “组织变革”。
德国西门子公司是工业4.0概念的发起者之一,亦是全球领先的数字化制造业企业。西门子成都工厂是世界经济论坛第一批“灯塔工厂”之一,该项目被誉为“智能制造的奥斯卡奖”。
从成都工厂的数字化转型经验来看,组织变革是制造型企业在技术升级基础上的重要转型任务,也是制造型企业数字化转型的必经之路。简单来说,成都工厂在组织层面经历了从外到内的两个变革过程。具体为:
过程一:组织外部较为显性的运营模式和决策模式的转变。即工厂从以专职数字化团队来推进数字化项目的“独立运营模式”,转变为以业务负责人来推进数字化项目的“融合运营模式”;从基于经验、中心化的“集中决策模式”,转变为基于数据和模型、去中心化的“下沉决策模式”。
过程二:组织内部相对隐性的管理模式和企业文化的转变。即工厂领导者从关注痛点、短期绩效和执行的“传统管理模式”,转变为关注机会、长期发展、创新以及人员成长的“新型管理模式”;从奉行高度执行力、最优绩效的“刚性企业文化”,转变为倡导以人为主、创造力和执行力相结合的“柔性企业文化”。
没有这两个层面的组织变革,企业的数字化转型就是无本之木。
成都工厂组织变革的成功有三大要素,其一是工厂自主设计的“数字化实施路线图”,其二是工厂始终坚持的“精益先行理念”,其三是工厂全力推行的“业务与员工双赢的创新机制”。这三大要素的形成,部分依托于西门子数字化工业集团“精益数字化工厂”计划,但更多源于成都工厂自身的业务发展需求和实践总结。
通过组织变革,成都工厂不仅成长为创新型组织和学习型组织,而且过去五年,在工厂蓝领人数增长100%、白领人数增长10%的情况下,工厂产值增长超过300%,工厂员工也从低价值的重复劳动中解放出来,成为兼具数字化思维和能力的数字化人才。目前,成都工厂的数字化转型已经从信息集成、知识积累阶段,逐渐迈向智慧运营阶段。相应地,工厂数字化发挥的价值也从机器代人价值、协同价值,逐渐升级为精准决策价值。
数字化转型的四大误区
近年来,数字化转型浪潮席卷而来,制造型企业对人工智能、大数据等数字化技术的应用如火如荼,但身处技术变革力量所带来的竞争压力之下,企业的数字化转型并非一帆风顺,多数企业尚处于推进“数字化”阶段,并未实现真正的“转型”。
具体而言,一方面,企业数字化技术的导入仅停留在示范“样板间”,未实现规模化应用;另一方面,随着数字化技术的导入和应用,企业并未在组织层面实现转型,这又导致数字化转型迟迟不及预期。通过观察和剖析制造型企业的数字化转型过程,我们看到企业往往存在四大误区:
误区1:重短期投入、轻长期规划。即企业注重短期投入而缺乏服务于其长期战略的数字化建设路线图。在相应误区下,企业数字化项目的实施与其运营目标脱节,导致基层员工看不到数字化项目的应用价值;数字化项目实施周期长、效果不确定,业务部门看不到中短期投资回报,进而怀疑其价值;各个部门各自为战也导致企业无法实现跨部门、端到端的协同,而数字化方案的效果,往往又离不开这种协同。
误区2:重技术升级、轻精益基础。即企业缺乏精益基础且未将精益制造的理念贯穿数字化转型的始终。在相应误区下,企业往往寄希望于通过数字化解决流程不精益的问题,造成很多浪费被固化在工厂生产运营中;在问题出现时,企业往往“头痛医头、脚痛医脚”,不追究也找不到问题的根源;企业在缺乏精益文化时,涉及运营模式、决策模式等的转型也很难推进。
误区3:重项目实施、轻人才成长。即员工数字化能力并未随着企业数字化项目的实施同步提升。在相应误区下,最了解一线问题的基层员工只是数字化转型的旁观者,他们既提不出高质量的项目需求,也无法胜任数字化转型后的岗位职责,导致项目周期长且效果差;项目结束后,基层员工并未掌握和驾驭新的数字化工具,内心更是不愿意接受数字化,导致企业无法持续迭代升级、进入自主创新阶段。
误区4:重效益提升、轻理念进阶。即企业把数字化当做效益提升的工具但忽略了在组织理念进阶方面带来的机会。在相应误区下,从企业领导者到基层员工均排斥转型,企业的数字化建设仅停留在以机器代人为代表的工具平台层面,即“黑灯工厂”阶段;相应地,企业的管理、文化等理念未做转型和提升,进而高水平的转型效果无法发挥,导致企业无法实现通过数字化转型提升竞争力的目标。
摆脱转型误区的关键:组织变革
深究其内,我们会发现企业陷入上述四大误区的绝大部分原因在于自身,即:企业仍然遵循传统发展逻辑,仅仅将自动化和信息化作为转型升级的关键,忽略了组织层面对于数字化的适配性变革,以及数字化人才培养的价值。
企业要想摆脱转型误区并在数字化时代脱颖而出,关键在于组织变革!我们认为,组织变革是制造型企业在技术升级基础上的重要转型任务,不仅能在“数字化”层面确保企业项目成功实施,更重要的是能在“转型”层面推动企业员工从高绩效员工成长为数字化员工。
本文所强调的组织变革,即企业从运营模式、决策模式、管理模式到企业文化的系统性转变,从而进化为创新型组织和学习型组织,如图1所示。具体为:
图1:制造型企业数字化转型过程中组织变革概览
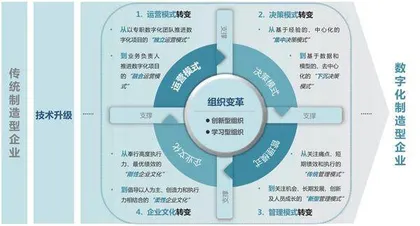
组织变革1:运营模式转变。即从以专职数字化团队推进数字化项目的“独立运营模式”,到以业务负责人推进数字化项目的“融合运营模式”。其中,独立运营模式下的专职数字化团队往往更关注项目落地而非运营目标的实现;融合运营模式下的项目团队,每个人都兼具两个角色,既是业务负责人也是数字化项目负责人,在业务运营目标的驱动下,既关注项目落地,更关注项目对业务产生的真正价值。
组织变革2:决策模式转变。即从基于经验的、中心化的“集中决策模式”,到基于数据和模型的、去中心化的“下沉决策模式”。其中,决策模式的转变涉及决策主体的变化,在集中决策模式下,决策主要由部门主管或工厂领导者(一把手)做出;而在下沉决策模式下,决策主要由一线人员结合数据和模型做出,不仅提升了决策效率,而且优化了决策质量。
组织变革3:管理模式转变。即从关注痛点、短期绩效和执行的“传统管理模式”,到关注机会、长期发展、创新以及人员成长的“新型管理模式”。其中,管理模式的转变也代表着企业领导力的变革,即企业领导者所具备的关于数字化企业发展的理念和观念,成为推动企业实现真正数字化转型成功的关键。
组织变革4:企业文化转变。即从奉行高度执行力、最优绩效的“刚性企业文化”,到倡导以人为主、创造力和执行力相结合的“柔性企业文化”。其中,企业文化的转变将极大程度地助力员工自我价值的实现,不仅让员工主动参与到数字化转型中、能力有所成长,而且让员工更有成就感。
组织变革的典型案例:西门子成都工厂
作为西门子数字化工业集团在中国的首家数字化工厂和世界经济论坛的首批灯塔工厂,成都工厂是数字化转型中践行“组织变革”的典型代表。成都工厂坐落于成都市高新西区,于2013年上半年建成投产,主要负责研发和生产工业自动化系列产品。近年来,成都工厂赋能员工不断自主创新,全面落地了数字孪生、人工智能、数据分析等数字化项目,并随着项目的实施推动了组织变革,将包括蓝领在内的大量员工,培养成了数字化人才,成功实现了数字化转型。
1.工厂数字化建设的三个阶段
成都工厂的数字化建设经历了三个阶段,分别是业务痛点驱动的数字化阶段、业务透明驱动的数字化阶段和业务智能驱动的数字化阶段,如图2所示。伴随着工厂数字化建设的阶段性成功,成都工厂也从“数字化工厂”逐渐迈向“智能工厂”。
图2:成都工厂的数字化建设历程
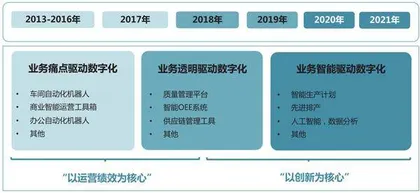
第一阶段:业务痛点驱动。该阶段工厂主要以“运营绩效”为核心,重点关注问题解决。即:通过推进与办公、生产等相关的自动化、数字化项目,解决痛点问题,持续提升生产效率,并将员工从低端重复劳动中解放出来。
以车间自动化和办公自动化为例:通过对已有产线的自动化升级改造,成都工厂不仅掌握了全自动产线的本地开发能力,而且有效提升了生产车间的自动化水平和生产质量;通过RPA、Mendix等低代码工具的导入,成都工厂最大限度地替代了与办公室相关的简单重复工作。体现在数据层面,则是年均5%-10%的简单重复工作被替代,尤其是在2016年工厂业务进入规模化阶段后,前期基于业务痛点的自动化、数字化项目开始真正产生价值——2016年-2021年,成都工厂蓝领人数增长100%、白领人数增长10%,而工厂产值增长超过300%。
第二阶段:业务透明驱动。该阶段工厂从以“运营绩效”为核心逐渐过渡到以“创新”为核心,更多关注透明带来的业务机会。即:通过数字化手段让工厂看不见的问题透明化并持续改进,随着工厂端到端协同的不断推进,员工也开始具备数字化思维,养成了使用数据说话的习惯。
以质量管理平台为例:通过质量管理平台,成都工厂不仅实现了所有生产线上全部质量数据的全制造流程“实时”自动采集和全价值链的集成,而且全方位地“透明”质量运行状态、100%追溯生产质量问题,从产品到材料、产线到工位等多维度实时呈现质量表现。
得益于质量管理平台的日常应用,工厂形成了“发现问题-解决问题”的质量管理闭环工作机制,从关注“是谁的问题”转变为关注“如何解决问题”,推动了产品质量的持续改善——产品缺陷率从建厂初期的百万分之8.4降至2022年5月的百万分之5.7。
第三阶段:业务智能驱动。该阶段工厂主要以“创新”为核心,关注基于数据的智能决策。即:通过不断迭代的算法,替代人的经验,建立集发现问题、分析、判断及自主决策于一体的科学系统,提升员工对业务的理解,进而辅助决策、自主决策。
以供应链风险预测为例:成都工厂日常生产涉及5000余种材料和上百家供应商,相应材料的供应风险识别和及时应对,对于工厂稳定经营至关重要。为此,成都工厂基于已有的原材料需求变化数据、供应商交付和质量表现数据,使用闭环优化的集成学习算法,对风险物料供应进行预测,并通过不断迭代对算法进行优化,找出最优风险预测解。