探索技术应用场景 小型飞行器设计研究
作者: 李锦山 赵健瑞 杨伟群引言
拓扑优化是根据给定载荷工况、约束条件和性能指标,优化初始构型材料分布的设计方法。可以在产品概念设计阶段确定产品最优材料分布。[1] 随着拓扑优化算法的成熟,商业化拓扑优化软件逐渐兴起,该设计方法已被成功应用与助推汽车、航空航天、材料等多个领域。[2, 3]
本项目将拓扑优化和增材制造两种技术结合[4],研究一体化设计制造场景下,小型飞行器的新型结构设计和增材工艺,从结构—材料—工艺三方面综合建模来研究各种不同拓扑结构形式下的结构力学性能和飞行性能,探索新型飞行器的设计与制作技术。使用低密度发泡PLA,应用FDM和FFF增材工艺,实现零件打印。
小型飞行器飞行参数获取
翼型数据获取
根据机翼三维模型获取数据点,将翼型数据导入XFLR5软件,进行分析。
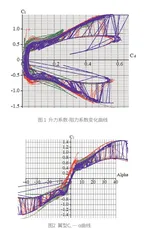
设置输出结果,开始分析机翼不同迎角下的相关气动参数的变化曲线,得到升力系数-阻力系数变化曲线(如图1所示)、翼型升力系数随迎角变化曲线(如图2所示)。翼型升力系数随迎角变化曲线(图2曲线)用于升力分析及迎角选择,进一步分析俯仰力矩,曲线有负斜率,翼型具有俯仰稳定性。
飞机结构及总体参数[5]
本文中的航模,采用鸭式布局。三角翼与机身融合保持了翼面的完整,有利于晶格设计。机身与垂尾采用抽插式设计,减小运输空间。
其几何尺寸为翼展600mm,机长530mm,机身长240mm,机身宽70mm。
气动分析
XFLR5是基于升力线理论,通过涡流晶格法,用于低雷诺数运行的翼型、整机分析工具。
为保证仿真测试的准确,在软件中建立气动模型与实际飞机等比例,设定分析空速同预期性能以确保运动相似,分析选取不同雷诺数范围以覆盖动力相似的范围。
在软件中依据模型设置几何参数,分析10m/ s空速下的整机气动参数,所得的分析结果如图3所示。
由图3得升阻比、升力系数均较大的迎角,取值约为6°,可作为安装角与飞行角度调整的参考。起飞选取10°~15°大角度以便升力充足。
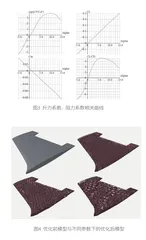
拓扑优化
该部分旨在针对载荷工况进行轻量化。依据受力与制造分块,相应拓扑优化分为两大部分:
(1)机翼及尾翼的格栅化处理;
(2)机身部分的格栅化填充。
机翼作为主要的受力部件,设定匀速飞行时的升阻力为载荷,基于此进行拓扑优化计算。机身在保证支撑强度的前提下,尽可能多地进行轻量化。
飞机各段拓扑优化
机翼格栅化处理
机翼部分通过多参数计算轻量化结构[6],经过分析,得到飞机平飞时的机翼载荷。即作用于机翼下表面的压强P1 =2.25×10-5MPa,作用于机翼前缘的风阻压强P2 =1.5×10-6MPa。
在该载荷工况下,以最小质量、1.2安全系数、格栅填充率100%为设计目标,改变格栅的长度L、最大直径dmax、最小直径dmin3个参数。部分优化模型如图4,经过后续分析获得对比评估数据如图5。
模型选择材料类型为尼龙材料,密度取值为1 . 1 4 g / c m3。设计前,机翼总质量M总 = m1+m2+m3 = 509.7g。将优化重点的质量数据绘制曲线,如图6所示。目标长度较小时,取得较低的优化质量。
综合考虑受载变形情况、应力强度分布情况、优化模型完整性、制造复杂度等因素(压力云图如图7所示),初步选用第五组格栅优化模型,即L=12mm,dma=1.2mm,dmin =2.4mm,飞机机翼部分减重至原质量的30.06%。
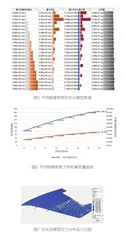
尾翼格栅化处理
尾翼部分设定载荷工况为:作用于尾翼前端的运动阻力。
尾翼优化进行了五组不同参数的格栅化处理,优化后的模型以及其性能相关参数如图8所示。尾翼优化前质量m初=35.384g,提取出优化后模型的质量有关数据与优化前模型进行对比,并绘制成表格如图9所示。根据表中图像变化看出,随着格栅目标长度的增加,优化后模型质量与优化后所占质量百分比随之增加。
由图中数据可以看出,第三组优化参数,即目标长度8mm,最小直径0.8mm,最大直径1.6mm的设定下,优化所得模型能够在保证使用强度尽可能高和加工难度尽可能低的情况下,总质量较多地减少。尾翼优化前后的模型如图10所示。
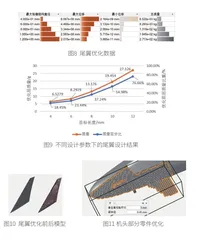
机身以及襟翼的格栅化填充
该部分主要受连接部位的约束与作用力,不易根据实际情况量化,采用参数化的格栅填充。主要依据优化后模型完整性与轻量化结果,选定合适的格栅尺寸与类型[体心立方(BCC)、简单立方(SC)、简单立方—体心立方(SC-BCC)、面心立方(FCC)、八角桁架(OT)、八面体桁架(TT)、K桁架(KT)、金刚石立方(DC)]。
考虑结构、工艺性、经济性后,优化部分零件结果如下。
机头部分选定单元格尺寸3 m m、梁半径0.45mm,如图11。该部分优化前总质量M1=827.9g,优化后总质量M2=252.4g,减重为优化前质量的30.49%。
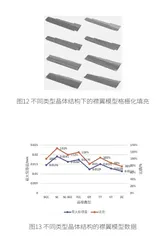
不同类型晶格结构下的襟翼模型经过强度分析计算,最大位移量以及相对于体心立方结构(BCC)最大应变比值,相关数据如图13所示。根据晶格填充的完整性以及最大位移量,金刚石立方(DC)为强度最佳结构。考虑制造的工艺性以及实际强度环境,体心立方(BCC)为最适结构类型。
整体优化结果及气动分析
飞机最终优化后的模型如图14所示,优化前总质量M0=1.8788kg,优化后总质量为M=585.26g,质量减少68.84%。(注:以上计算均是基于尼龙材料,ρ=1.14g/cm3,与打印所用材料不同。)
飞机的整体设计优化均是基于Inspire软件平台进行处理,所得到的轻量化设计后的模型符合轻量化设计要求的设计目标,并在强度设计上符合实际强度要求,同时设计也兼具航模飞机制造的可行性与经济性。
拓扑优化设计后的飞机变化的参数导入XFLR5软件,进行气动分析处理。结合实际情况和必要理论估计,设置相应的飞行参数。
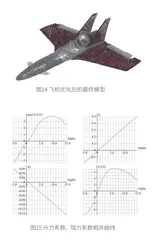
最终所得到的飞机设计模型,飞机飞行时的升力系数、阻力系数相关参数曲线如图15所示。优化前后飞机气动数据对比如表1所示,在最适迎角6°的情况下,升力系数和升阻比均有提升,由于机身、机翼质量减轻,整机重心前移,稳定裕度取得83%的提升,飞机稳定性有所提高。
增材制造
主要使用LW-PLA线材,结合FFF与FDM技术,实现复杂格栅化模型与部分壳体的3D打印。
主要材料
PolyLite?LW-PLA,作为零件原材料,参数如表2。其发泡率随温度变化,在打印温度240℃时ρ=0.69g/cm3,可据此估算其余参数并用于强度校核;水溶性PVA,作为复杂晶格的支撑材料,便于去除。
零件制造
设备选用上海远铸公司开发的FUNMAT PRO 610 HT工业打印机,尺寸、温度可以满足高性能热塑材料的一体化机身和机翼打印。包含两个喷嘴,可以实现支撑与主体两种材料的同时打印。

参考已有研究结果[8-10],经过实际打印参数调试,最终确定相关打印参数如表3所示,该参数下的打印件表面天然哑光、强度符合实际应用场景要求。
对于拓扑优化后的格栅化零件,其结构上存在多处悬臂格栅以及复杂晶体结构。如果直接进行3D打印制造,将会产生大量拉丝,增加后续零件的处理工作量。我们采用水溶性支撑结构,降低了模型损坏的风险,考虑PLA材料的热变形温度,取约45 ℃水溶液实现去除。[7] 打印结果及PVA材料的去除后的零件如图16、17所示。
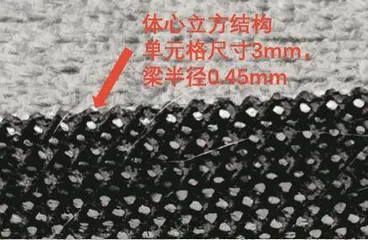
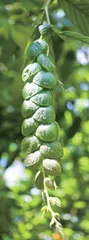
飞行器整体分析与试飞
飞行器整体分析
经过拓扑优化的轻量化设计以及低密度材料的增材制造,小型航模飞行器机架减重至163.9g,实现了飞机轻量化的目标。具体零件质量如表4所示。
装配必要的控制装置、动力装置、连接件等,最终实际装配的飞行器质量为424.1g。装配后的整机如图18所示。
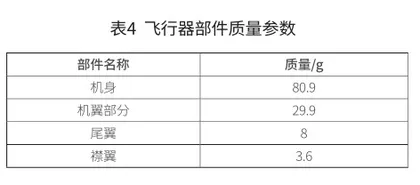
飞行器试飞
飞行器在室内吊挂进行飞行姿态调试,调试过程中,飞行器有明显的上升姿态,动力系统能够为飞机提供必要的升力。
飞机经过室外试飞,能够满足航模飞机优化前的飞行要求,在气动分析中的10m/s设定速度下能够实现飞行目标。飞行器经过轻量化处理后,飞机整体强度基本满足实际要求的同时,飞行性能有所提高,实现了飞行器的轻量化处理,完成了该项研究既定的研究目的与设计目标。
总结与展望
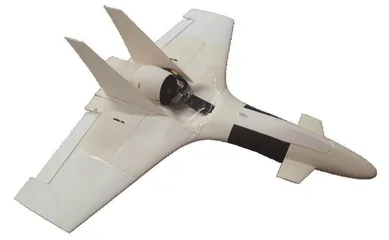
本项目将现有小型飞行器进行轻量化设计,结合拓扑优化和增材制造两项技术,实现小型飞行器的新型结构设计和增材工艺应用。在满足基本强度要求的基础上,轻量化设计后的飞行器重量更轻、抗摔性更好、模型可修复性更强、飞行性能更好。