

一滴酱油的“风味之旅”
作者:张从志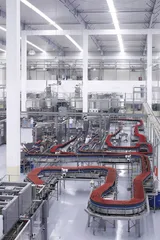
要了解中国酱油产业的运作方式,高明厂是合适的造访对象。它的全称叫海天(高明)调味食品有限公司,是海天味业(以下简称“海天”)旗下最大的生产基地,位于广东省佛山市西南的高明区一处工业园内,离市中心有50公里左右。这里安保很严,访客进出要提前预约,查验身份。整个厂区有1300多个监控探头,24小时有人值守。
但是,如果你对酱油有足够的兴趣,通过公开的渠道也可以预约进入参观。为此,高明厂建有一条全长超过2公里的回字形空中走廊,连接着工厂核心的功能区,走一圈就可以看完酱油生产的全过程:从原料黄豆进来,到蒸煮、酿晒,再到包装出厂。虽然隔着玻璃,但也颇为壮观。这是这家工厂关于工业旅游的部分,它最早的落地可以追溯到2005年该厂一期项目投产之时。在那个时候,一家酱油厂开门迎客确实还是较为超前的实践。如今,整个参观走廊的设计仍是当年的亲子风格,在过去十几年中,已经接待过近200万名访客。
参观的起点是一处展厅,地板上嵌了一块金属铭牌,上面刻着一条“北纬23.18度”的纬度线,后面还写着“紧靠北回归线,属于热带,每年太阳直射2次,是酱油晒制发酵的理想地带”。佛山自古多酱园,海天的前身就是建国后公私合营时期由20多家酱园合并而成的一家酱油厂。其实在珠三角一带,不只是佛山的海天,还聚集着另外几大酱油巨头,比如香港的李锦记,其最大生产基地设于江门市新会区;还有中炬高新旗下的厨邦酱油,大本营在中山市。要算产量的话,广东省能占到全国酱油总产量的60%多。广式酱油如此受欢迎,除了和强势的粤菜文化有关,正如地上这块铭牌试图传达的:阳光,也在给出答案。
好酱油是晒出来的,这是吃了上千年酱油的中国人固有的观念。近些年,随着大家健康意识的提高,各大酱油厂商都在不遗余力地强调自家产品经过了如何长的晒制时间。海天也不例外,他们很早就喊出了“不止晒足180天”的口号。
一年260多万吨的酱油,到底是怎么晒出来的?在空中走廊的中段,我们看到了一个巨大的酱油酿晒场,在生产过程里,这是耗时最长的环节。海天用来晒酱油的设施如今分两种,一种是玻璃晒池屋,一种是发酵罐,它们加起来的占地面积超过60万平方米,相当于70个足球场大小。这个地方被海天的人形容为“阳光海洋”,有点浪漫化——这的确是全世界面积最大的酱油晒场。佛山的阳光挺毒辣,3月上旬,北方还是风寒料峭的时节,这里一到下午就晒得厉害,在晒场里走动的工人都要用帽衫把自己裹得严严实实。旁边的一名工作人员说,他们刚进海天时都要下工厂实习,巡查晒场是很多人觉得最难熬的工作,尤其是在夏天的时候,涂多少层防晒霜都不管用。
玻璃晒池,其实就是一个个的水泥池子,最小的面积约18平方米,高约1.7米,最大的面积约40平方米,高约3.7米,内壁和外壁都贴了白色瓷砖,顶上盖的是带有一定倾斜度的透明玻璃。据介绍,其角度也是经过设计的,以便池内有更好的光照。池子密封着,只留了很小的排气窗,进料出料都是靠管道输送。这样的玻璃晒池,晒场里有数千座。不同的池子里装着不同发酵阶段的酱醅,一开始是半固态,随着时间的推移,逐渐液态化,颜色也变红、加深。有时隔着玻璃,我们仍然能闻到池子里散发出的酱香味,那味道有时很淡,有时则十分浓郁。酱醅在池子里发酵6到9个月后,变成酱油原油,工人就会把原油抽取出去,然后清理掉池底的酱渣。
玻璃晒池的缺点是无法翻动,所以工厂有了升级版的立体发酵罐。那是一种银灰色的储罐,高达十来米,笔直地立在晒场里。讲解员说,这种罐体用的是一种特殊材质,阳光直射灌顶,在光和热的作用下起到酿晒的效果,而且罐子里装了搅拌器,可以让里面的酱油可以更加均匀、充分地发酵。
沿着这条走廊走一圈,花了我们两个多小时,直到参观完最后的灌装线,我们也没接触到一滴酱油——除了最后吃到的一个微微带点咸味的酱油冰淇淋。带我们参观的人说,别说访客碰不到,车间里的工人也碰不到一滴酱油。而且在高明厂里,他们引以为傲的准则正是:人不能接触到产品。自从黄豆进了原料筒仓,后面所有的生产环节都封闭了起来,连接它们的是不同粗细的管道。
如果非要找到一些例外,徐敏杰是其中一个。他负责的设备维护部门是整个工厂唯一可以在产线上实际接触到酱油的部门。设备维护人员24小时轮班,他们的任务是保证产线的正常运转。当机器进行检修或发生故障时,他们就要去拆装设备,由此便可能接触到管道里残留的酱油。徐敏杰苦笑说,有时穿着工服下班回家,孩子都能闻到他身上浓郁的酱油味道。
徐敏杰是广东湛江人,1976年出生,穿着灰蓝色的工装,说一口粤味普通话。1998年从广州轻工业学校电气化专业毕业后,他跑到佛山找同学玩,同学家在老城区,离当时海天在禅城区的老厂不远,那边的街坊邻里都是闻着酱油味长大的。徐敏杰听说这家企业不错,于是跑到工厂门口,跟门卫打听还招不招人,门卫也好心,把他领了进去,最后推荐到了一个领导那里。对方看着眼前的这个青涩、内向的小伙子,让他回去写个简历寄过来。就这样,1998年7月13日,徐敏杰进了海天。1998年是个特殊年份,这一年,海天开始大批量招收大学毕业生,将他们补充进销售和生产研发队伍中——这是要大举扩张的信号。
和徐敏杰一样,学工业发酵专业的冯骏也是1998年进入海天的。他参加了当年的校招,和他一批进来了很多人。按照传统,他们都要先下车间实习几个月。冯骏去的是文沙老厂,这是海天起家的地方,位于佛山市禅城区文沙路16号,马路对面就是佛山第一中学,过条小河是中山公园。在产线上,从挑选黄豆、清洗、蒸煮,到酱油酿晒、灭菌、包装,冯骏全都做过。那时候,海天的工厂里还能见到特别传统的生产方式,比如瓦缸酿晒,一个缸几十上百斤,搬起来要人命。
上世纪90年代末期,海天的主要市场仍在珠三角区域,一年的销售额不过七八亿元,总产能十几万吨。但从1998年开始,接下来的十几年里,海天保持了年平均15%左右的增长率。每过几年,规模就上一个量级。在这种态势之下,文沙老厂的生产线已经满足不了市场的胃口。
而且,随着佛山的城市发展,一个大型酱油厂身处禅城这样的核心城区,在闹市之中,从各方面来看都显得不合时宜。工厂的环保问题,物流周转,还有发展用地都是摆在眼前的难题。于是,搬迁提上议事日程。去野心勃勃的高明区,在当时也是顺理成章的事情。高明区在佛山市的西南部,跟肇庆市接壤,原本是个小县城,县改区后,最富余的就是土地。听说海天要建新工厂,高明区一笔就划了3000亩用地给海天。
“一张白纸任你画”。对于当时的海天决策层来说,问题在于,这个工厂要怎么建。“我们可以把文沙厂照搬过来,复制粘贴,也可以重新规划,做些不一样的事情。”冯骏说。
一开始,决策层决定,步子不能迈得太大。2003年,高明一期工程破土动工,规划产能是30万吨。冯骏是2004年被调到高明来当厂长的。2005年,高明厂一期正式投产。“一期30万吨做完以后,它相比我们文沙的老厂已经有不少改进,但它还不是颠覆性的。”冯骏回忆道。在他到公司的前十来年里,老是感觉供不应求,产能拉满还是很紧张。“每年过年我们都要加班,很少在大年二十九之前回去,再靠以前那种以人工为主的生产模式,已经吃不消了。”一边是神经紧张的生产部门,一边是如饥似渴的销售部门。等到2009年,高明厂二期工程动工时,原本年产30万吨的产能规划已经被改成了300万吨。
量的飞跃,意味着生产体系要发生质的变革,需要的是新技术和新装备。“做酱油,其实就是一种叫米曲霉的微生物将黄豆里的蛋白质转变成氨基酸的过程。我们对这个过程研究了很久,了解米曲酶在生长过程中需要的温度、水分和氧气。后来,我们还画出了一条米曲霉的生命曲线,可以根据这条曲线,来控制温度、氧气或者水分。”冯骏强调,这种控制在之前那种敞口的生产环境里是无法实现的,所以装备的支撑很重要。
和酿酒一样,酿酱油也有个制曲的环节,把蒸煮的大豆与小麦粉混合到一起,再加入米曲霉等菌种,制成曲料。我们从空中走廊经过制曲车间时,要使劲扒着满是水雾的玻璃,才能窥见里面的情况,整个车间是圆柱形的,分成上下好几层,曲料都铺在一个个大圆盘上,里面的温度据说能达到五十度,即使隔着厚厚的玻璃,手都能感到热量。冯骏向我介绍,这就是圆盘制曲,这种技术最早是国外企业发明的,但他们的装备尺度小,海天要上大规模生产,自己研发,最后把圆盘的直径做到了20米,是全世界最先进的圆盘制曲技术。“这种技术颠覆了以前传统的高层制曲池。现在一个圆盘单次就可以制曲超过50吨,以前要几十个曲池才能做到。”2007年,徐敏杰也被调到了高明厂,在这里,设备升级换代的速度有点超出他的预想。他当初刚进公司的时候,大部分工序都是手工生产,需要专人维护的设备并不多,灌装车间里的机械设备最多,而且用了很久,常常坏,所以他被分配到了那里。但到高明后,灌装线已经用上了从德国进口的新装备,全自动化,说明书都是英文的。为了搞懂里面的技术细节,徐敏杰不得不开始苦学英文。在一般的工厂,设备维护都是幕后部门,存在感不强,但在高明厂,徐敏杰可是重要角色。“我们在生产线特别紧张,压力也很大。整个灌装线现在一个小时能生产差不多5万瓶酱油,不用说停一天,停一个小时就不得了。”
高明厂二期于2012年正式投产,这一年,海天也启动了上市计划。对高明厂的改造,则仍在继续。“传统的生产方式,从黄豆挑选到最后灌装,每个工序都是分离的,中间要经历6到9个月的时间,在这么长的时间里,一是需要非常多的人工;另一点更关键的是,各个环节都有可能存在污染的风险。”公司一位高层李小丽说,他们花了好几年时间,才把整个生产工序全部连贯起来,实现连续化生产,从而使得整个生产过程人都不用接触产品,甚至设备和管道的清洗都是机器设定好的。这种生产模式,既可以降低食品安全的风险,也能进一步提高生产效率。
冯骏介绍说,现在高明厂总共有3300多人,其中生产一线的员工约2000人,每年都在减少,而工艺研发、设备管理和科研人员每年都在增加。“我们前些年一条灌装生产线一个小时产24000瓶,现在一条线一个小时产52000瓶,产能翻了一倍多,但用人只有原来的一半。”支撑产能扩张的,是不断增长的市场订单。海天从佛山一个地方性品牌变成全国调味品巨头,其中无法绕开的一个人物,就是海天味业现在的董事长庞康。在业内,庞康是极其低调的一个人,多年以来,关于海天的新闻,他几乎从不出面回应。这种低调,也成为这家公司上上下下的一种行事风格。在我们采访过的人里,不少人都提出了化名的请求,还有的人是实在推不掉才答应坐下来聊聊。他们似乎都秉持着埋头做事的信念,他们也希望传达给外界这种印象——只不过,有时候并不成功。
近年来,随着海天味业在股市上市值的飙升,低调已经很难维持下去,庞康更是成为各大富豪排行榜上的常客,排名每次提升,都吸引着舆论的目光。2020年9月1日,海天味业市值突破6000亿元,把万科、中石化等一众各行业巨头甩在身后,一些企业家公开调侃道:“卖房子不如卖酱油。”尽管后来市值回落,但海天味业从此有了“酱茅”的称呼。作为行业龙头,它每一次公告提价或降价,整个调味品行业都得被牵动。
庞康于1956年出生于广东佛山,1982年,从南京师范学院食品机械专业毕业后,他被分配到佛山珠江酱油厂(海天味业前身),从一名普通技术员开始了进阶之路。大约6年后,他已经做到了酱油厂的总经理。在他手里,酱油厂经历了改制、扩张,慢慢地从珠三角走向全国。
这个过程中,庞康展现出自己的决断力。1998年,海天开始大举招聘大学生,组建了一只上千人的销售团队,开始在广东以外的区域开疆拓土;1999年,海天在《新闻联播》整点投放广告,成为第一个登陆央视黄金时段的酱油品牌;2003年,海天在销售会议上确定了“全面开发县份市场,启动农村销售”的销售政策,并于同年着手推动县份市场经销商开发。这一年,文沙厂还引进了德国的自动罐装线,包装速度提升到每小时24000瓶。扩张产能,配合全面营销,每一步,都踩在点上。
进入21世纪后,中国餐饮行业迎来自己的黄金时代,餐饮标准化逐渐成为趋势,各种连锁品牌涌现,餐饮的市场规模膨胀到万亿级别,那时候,就连厨师烹饪学校都生意火爆,成了电视台主要的广告金主之一。而酱油作为中餐烹饪里最常见的调味品,自然搭上了这趟增长快车。
2005年进公司后,湖北人陈志很快就被派到了销售一线,最初是在广东,然后上中原,最后进了北方大区。不同的地域有不同的菜系,口味各异,陈志早年跑市场要做的一件事就是跟餐厅里的大厨和采购经理打交道,尽可能搜集他们的需求。“比如有的地方喜欢吃清蒸鱼,我们就推广蒸鱼豉油;有的地方爱吃酸,我们就推凉拌醋。”陈志说,消费者对产品品质的要求是第一位的,但不同的市场需求也有区别,比如B端的餐饮行业看重性价比,而且包装规格要大,而C端一般都是家庭主妇在购买,使用便捷性就很重要,小包装更受欢迎。还有一些需求,则是企业在背后推动的。比如生抽和老抽的概念,最早全国很多地方的消费者都不明白,他们到超市里,只会说我要买酱油。海天的市场团队便通过各种方式去推动消费者建立认知,告诉大家生抽和老抽颜色上有什么区别,用法有什么不同,慢慢建立了一套产品体系。到现在,全国人民都知道,炒菜凉拌用生抽,红烧用老抽。由此海天得到的回报是,金标生抽和草菇老抽最早成为过10亿元销售额的爆款单品,并且至今畅销不衰。
陈志如今是北方营销中心总经理,据他介绍,目前海天在全国有6000多家经销商,整个销售网络最低触达到了村镇。他们有句话叫“有人烟处必有海天”,正是通过这张庞大的网络,各种信息源源不断地汇集到产品研发和生产部门。
从珠三角走向全国,反过来也给冯骏负责的工厂带来了好处——在时间维度上,他的生产计划变得更均衡。他刚进公司的时候,酱油厂的生产季节性特别强,过年前最忙,过完年以后闲下来。“因为以前我们的市场集中在珠三角,过年前这段时间,市场很火,到过年,外来务工的人都回去了,市场自然冷下来。等我们的市场铺到全国,就不一样了,外省的人从广东回去,在当地还是要买酱油,所以我们的销售和生产节奏就相对拉平了。”
这是冯骏作为工厂管理者乐见的局面——“我们生产追求的目标就是良性的满负荷运行,尽可能地提高我们的产能利用率,产线不停,设备利用率就高,整个人员队伍的稳定性也会提高。”而身为厂长,做计划过去非常消耗冯骏的精力。以前他是酱油厂厂长,在他后面还有包装厂厂长。“我这边做计划,就要跟他们那边打电话沟通,我生产10吨或者20吨,你那边接不接得了。现在我们上了智能制造的系统,所有的计划都在上面打通,可以等订单来了再排产。从管理上来说,比以前轻松了很多。”
这样一来,工厂的周转也会加快。在高明厂内有几个五颜六色的巨型仓库,他们称之为“立体彩仓”,里面一次性可以存放几十万箱产品,只要在系统上下达指令,箱子就会沿着纵横交错的轨道自动进出。“以前我们的货放在平仓里,都要靠人用叉车去叉出来。你责任心再强,货堆得多了,有时候也会忘掉。时间一久,产品就可能过期了。现在,我们每一批入库的货,都有一个条形码,把身份信息录入系统,系统会根据订单的需求,自动生成指令,把货调出来。”冯骏说。因为调味品都有保质期,对下游的经销商来说,他们尤其关心产品的“新鲜度”。“日期太旧,他们是不喜欢的。”冯骏告诉我,现在大宗的产品一般不会在厂里存放超过一个星期,小宗的产品时间可以长一点,但一般30天系统就开始预警了。“最快的我们能做到,今天下线,明后天发走。现在我们的产品品类越来越多,算SKU的话接近上千个,如果没有信息化系统做支撑,你要疯掉。”风味的奥秘
在传统的生产环境下,做酱油也是一个看天吃饭的行业。“因为我们要利用阳光,但阳光并不稳定,有阴天有晴天,有冬天也有夏天。我们不能跟消费者说,这个月的酱油不太好吃,咸一点或淡一点,是因为最近佛山阴天多。消费者需要的是你生产出的每一瓶酱油必须是一样的品质。”李小丽谈到,为了达到这一点,菌种和工艺研究很关键。海天现在有6000多名员工,其中1000多人都属于技术人员。
刘海洋是菌种研究院的院长,2009年,他在研究生毕业后进入研究院工作,最初这里只有二三十人,后来人员不断壮大,现在整个研究院已有80多人,60%以上都是研究生学历,还有多个博士毕业。刘海洋介绍,菌种研究院的工作分成了三大板块,即底层技术研究、菌种选育和产业化应用,这三块也对应着菌种研究的三个阶段:选菌、培育、投入大规模生产。
“酱油发酵过程涉及的菌种主要有三大类,一类是米曲霉,一类是酵母,还有一类是乳酸菌。其中米曲霉是主要功臣,它会把黄豆中的蛋白质分解成氨基酸和小分子肽,而这是酱油色香味的主要来源。”刘海洋告诉我,传统酿造行业其实有一个由成千上万的微生物组成的非常庞大的菌种资源库,只是以前大家没办法把里面的菌种都识别鉴定出来,搞清楚它的原理,以及哪些菌种有用,哪些没用。这个工作就是他们研究院现在底层技术研究团队在做的事情。
通常来说,找一个好的菌种,刘海洋主要关心三个方面。“一是它要美味,通过它能将原料里的鲜味组分呈现出来;二是要特别稳定,只有稳定的菌种,才能够支撑大规模生产,保证每一批产品品质的稳定;三是要有较高的转化效率,通过它能把黄豆和小麦里的营养组分尽可能多地转化到产品里去。”刘海洋继续道,“菌种也是一个生命体,和人一样,有的人擅长长跑,有的人擅长短跑,有的人喜欢寒冷的环境,有的人比较适合温暖的环境。酱油生产也会历经季节和温度变化,所以在不同的时节,我们也要对菌种做出调整。”
菌种在制曲车间加入生产过程后,会经历一段漫长而复杂的变化。以前在瓦缸里发酵时,这个过程人为干预很少,但上了工业化生产,就需要将整个生产工艺固定下来。当初招进来的大学生,经过专业的系统训练后,在其中发挥了主导角色。他们的任务就是要把以前老师傅留下的经验做成一整套工艺标准体系。
“我记得一开始的时候,我们一道工序可能就两页纸,后来变成10页纸、几十页纸,不断地细化、标准化。”冯骏说,这一步非常重要,没有这一步,后面整个产线的自动化和智能化升级也不可能完成。
今年44岁的王君安是酱油事业部的负责人,河北人,本科和研究生学的都是食品工程专业。他在2005年加入海天后,将近十来年的时间里一直从事工艺技术研发。和所有刚入职的大学生一样,他也是先下车间,跟着老师傅做酱油。以前很多知识都是课本上学来的,到了现场,他看到的是不一样的东西。“老师傅用鼻子一闻,用手一摸,看看颜色、体态,就知道池子里发酵得怎么样了。很厉害。”
但是,王君安过来可不完全是跟老师傅学手艺的。传统的那种经验导向的生产模式,在规模急速膨胀的海天,已经走到了悬崖边上。“举个例子,我们做酱醅,需要用曲料和盐水混合,最开始都是靠人的经验,就像厨师做菜一样,加一勺盐或者少许盐。”王君安介绍,“包括发酵环节,以前是自然结菌,就放在那里,长成什么样子就是什么样子,废了就废了。所以你做100批产品,里面就可能有几批是不太成功的,或者风味会有差异,特别是夏天和冬天,批次间的波动就大。”
王君安他们要做的事情,就是借助各种手段,弄清楚每道传统工艺的原理,然后做出改进。比如酱油里面到底有哪些成分,哪些成分好了,它的味道就会好;还要引入一些设备,比如用流量计来测定盐水和曲料混合的比例,以对其进行精准控制。而且有些工艺在实验室里做出来了,效果很好,但放到大生产中又不一定,因为它还要和生产用的设备结合。“举个简单的例子,你煮一锅水,在实验室拿个烧杯或壶去煮,很快,受热均匀,但拿到锅炉里,就完全不一样了。”王君安说,“所以,我们对员工的要求其实更高了,以前不需要什么学历,搬搬抬抬,甚至不识字都没问题。现在你可能要懂点理论、懂点程序,学历要求也会慢慢抬高。”
所有的硬件和软件升级,最后都归结到一点,就是要不断地提高生产效率,最后转化为企业竞争力。“比如说一粒黄豆,我们的转化利用率是90%,别人只能做到80%,你只要高10%,一年几十万吨,最后形成的就是显著的成本优势。”冯骏说,这就是海天的毛利率能在行业内保持较高水平的关键。特别是疫情这几年,黄豆、小麦粉、白糖等原材料的价格涨幅都很大,成本优势就更加重要。
但对于一家长期稳坐船头的企业来说,危机总是埋伏在前方。近几年,不管是终端还是渠道,都在发生巨变,整个调味品市场的竞争越来越激烈。特别是随着C端家庭消费的占比提高,消费者对酱油产品的需求更加细分,无论是追求健康化还是高端化,都正在创造新的市场机会。对过去较为倚重B端的海天而言,如何抓住新的机会,永远是一道思考题。
(实习生方厚寅对本文有贡献,文中冯骏、李小丽、刘海洋、王君安为化名) 海天食品酱油